MODELOS Y ENTORNOS DE APLICACIÓN DEL SGL (SISTEMA GESTION LEAN)
El sistema de gestión Lean (SGL) podemos implantarlo a distintos niveles de la organización, y es lo que vamos a denominar modelos.
Lean Strategy & Lean Management:
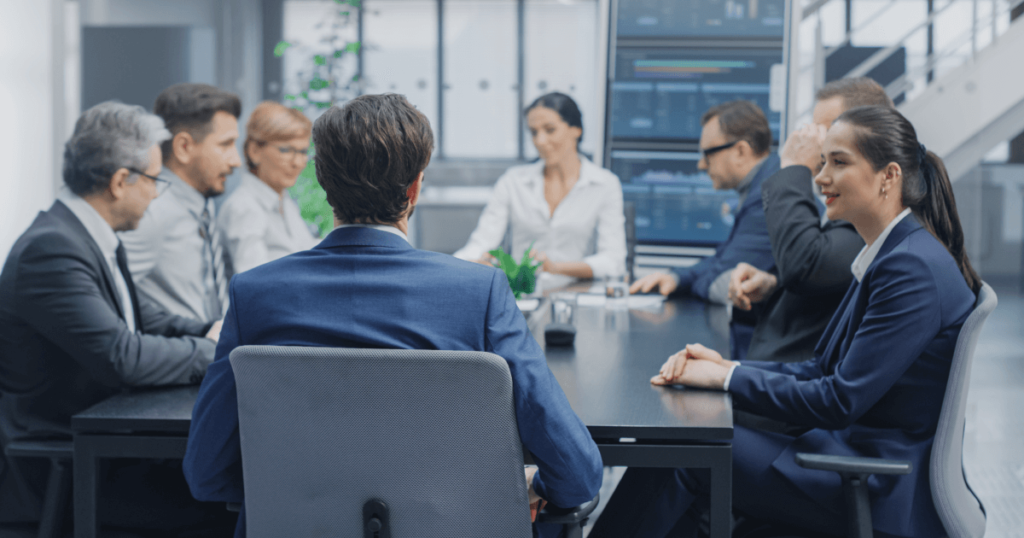
Es la aplicación de la metodología LEAN a nivel de la estrategia global de la empresa, a nivel de la dirección de la empresa, y es de la que debe emanar todas las decisiones e implicación para que esta herramienta de mejora continua sea un éxito y no un fracaso.
Los objetivos estratégicos del negocio deben estar en consonancia con los trabajos que realizan nuestros equipos.
Por lo que podemos decir que hay 3 niveles: los objetivos de dirección, los estratégicos que lideran los directivos de la empresa en un segundo nivel y los que afectan al tercer nivel o núcleos operativos de la empresa, que son los responsables de producción, calidad, almacén, mantenimiento.
Vamos a conseguir con este modelo:
- La implantación global de la metodología Lean y la ejecución excelente de la estrategia del negocio. Definir los objetivos de la empresa.
- Definir y desplegar la estrategia a todos los niveles de la empresa.
- Asegurar la ejecución de la estrategia.
- Definir e implantar una organización estructurada, alineada y motivada.
- Estructurar y mejorar la cadena de valor del negocio y sus procesos.
Existen distintas herramientas para aplicar en Lean Strategy.
Aunque sería el primer modelo por donde deberían empezar las empresas, lo habitual en las empresas que se acercan al la metodología Lean, es que empiecen por el entorno productivo (Lean manufacturing).
Lean Manufacturing:
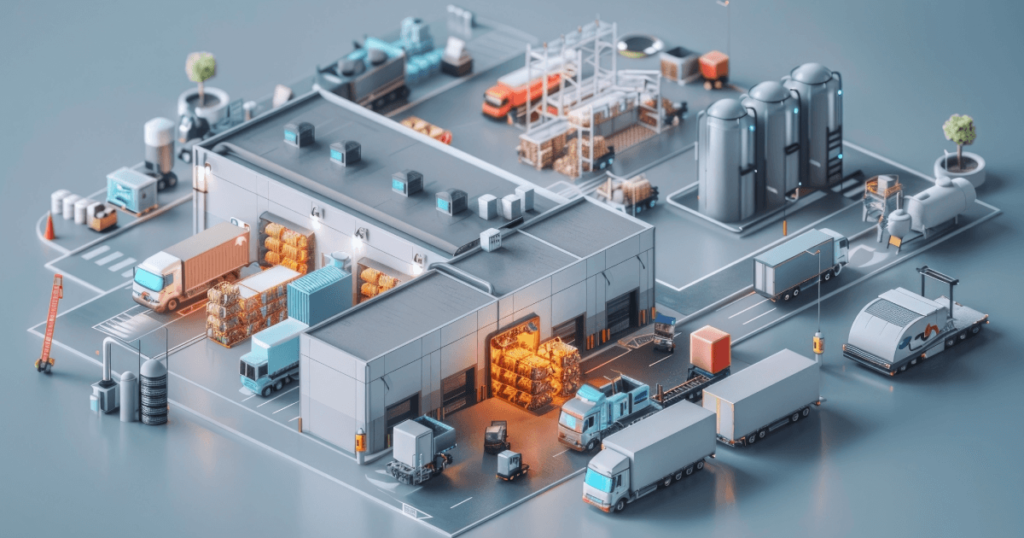
Es un modelo con enfoque a procesos altamente repetitivos, y donde prima la gestión del núcleo operativo.
Nos va a servir este modelo para:
- Reducir costes y generar ahorros en mano de obra, máquinas, consumos y materias primas,
- Reducir costes de no calidad y mermas…
- Mejorar la calidad de los productos.
- Mejorar la implicación de los empleados: con una buena organización y jerarquía enfocada a la mejora.
Se va a disponer de números indicadores, ya que se que generan muchos datos en poco tiempo.
Existen números herramientas Lean específicas para desarrollar con los equipos de producción.
Lean Office:
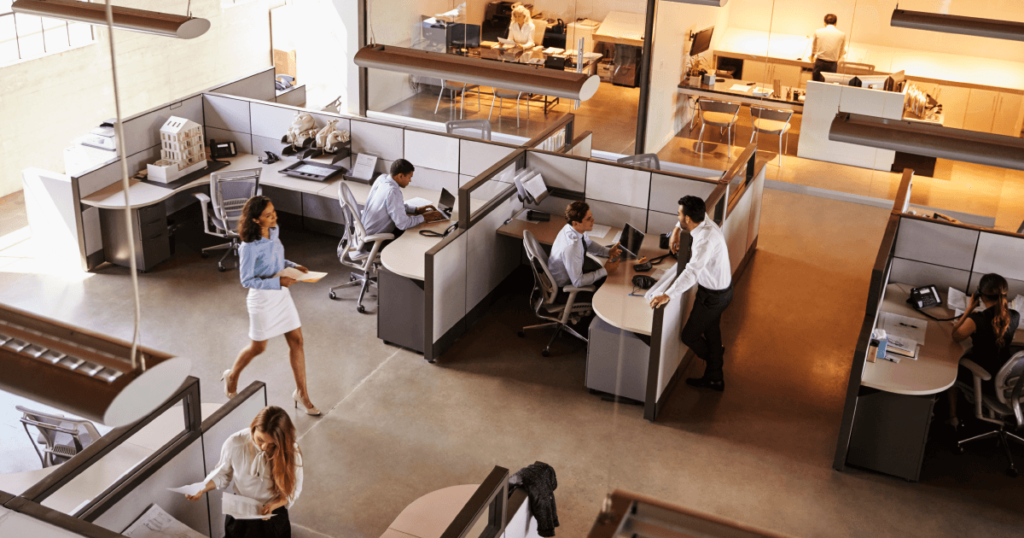
En este caso el modelo se va a enfocar a la gestión de procesos que ocurren de forma transversal en la empresa, en la cual habrá relaciones entre departamentos. Ej_ Departamentos de calidad, RRHH, administración, informática.
Con este modelo podemos alcanzar los siguientes objetivos:
- Reducir costes y generar ahorros en tiempos de respuesta, reducción de incidencias, mejora de ofertas…
- Mejorar la calidad de los procesos.
- Mejorar la implicación de los empleados: Organización y jerarquía enfocada a la mejora.
Sobre todo, se aplicarán herramientas de flujos de trabajo.
El volumen y frecuencia de reuniones será inferior al de Lean Management (entornos productivos).
Lean Project:
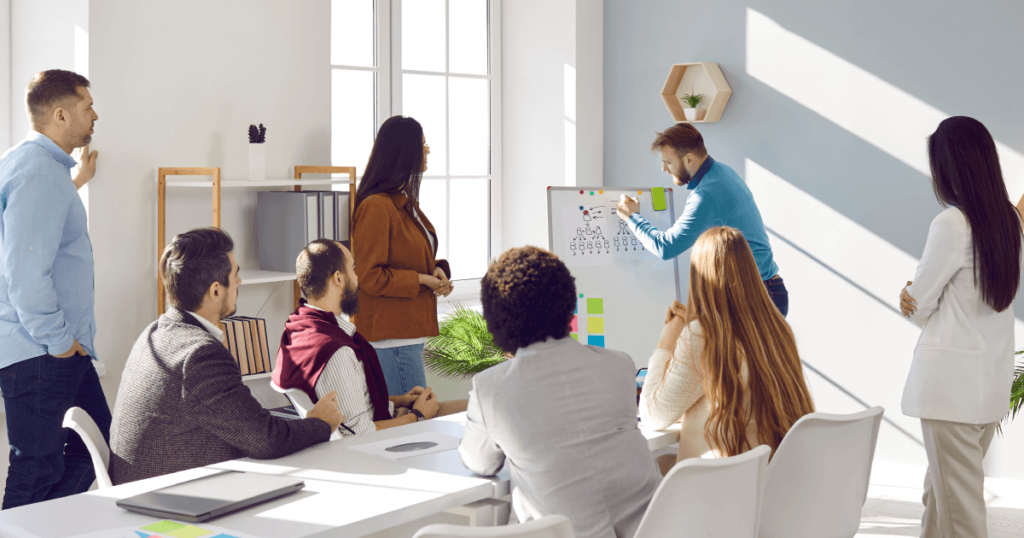
Al basarse en proyectos este modelo, tiene el fin de conseguir un solo resultado en cuanto a cumplimiento de costes, plazos y fechas definidas con sus responsables correspondientes.
Es el modelo ideal para departamentos de I+D+IT, de ingeniería de producto o de proceso.
Aquí es importante el control de la fase de proyecto, los hitos del cronograma, los entregables de cada responsable, el seguimiento o porcentaje de cumplimiento de esos hitos.
Los objetivos que podemos conseguir al usar esta metodología son:
- Reducir costes y generar ahorros en el cumplimiento de planes de proyectos, gestión de recursos, enfoque a resultados…
- Mejorar la calidad de los proyectos.
- Mejorar la implicación de los empleados: Organización y jerarquía enfocada a la mejora.
Dispondremos de técnicas específicas para desarrollar en estos proyectos.
Lean Leadership:
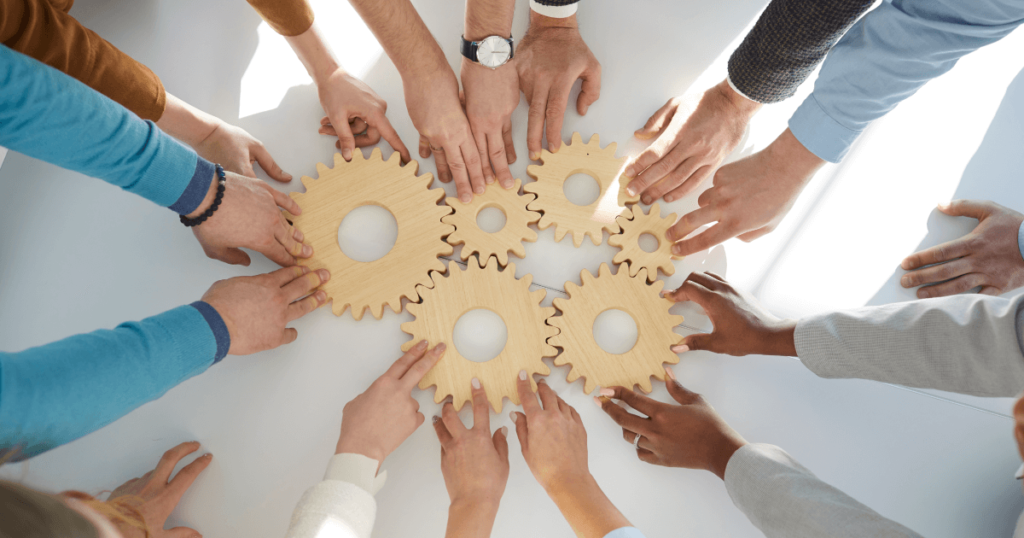
Modelo basado en la gestión del desarrollo personal, ligado a la motivación de los trabajadores y liderazgo de los gestores en todos los niveles.
Aquí vamos a poder usar otras herramientas como el Coaching ejecutivo y el de equipos.
Con este modelo podemos obtener:
- Habilidades necesarias para el liderazgo.
- Equipos más cohesionados y productivos.
- Mejorar la satisfacción personal de los trabajadores en su puesto de trabajo.
- Mayor compromiso de los empleados con la empresa y la estrategia de la misma.
IMPLANTACIÓN DE UN SISTEMA LEAN
La implantación global del Sistema Lean es una decisión estratégica tomada por la dirección de la empresa. Los objetivos generales que tendremos al implantar este sistema son:
- Definir y cumplir la estrategia del negocio, aumentando su competitividad, y mejorando su balance económico.
- Provocar el cambio cultural de todas las personas de la organización hacia la mejora continua.
- Crear el propio sistema de mejora continúa adaptado a cada empresa para conseguir una consolidación en el tiempo, y evolucione dicho sistema y la empresa hacia la “Excelencia empresarial”.
El éxito de la implementación de estos sistemas es que debe ser algo que sea elegido y liderado por el CEO o propiedad de la empresa.
Hay que saber que para que el sistema funcione habrá que provocar un cambio cultural en la organización, porque vamos a implementar nuevos sistemas de trabajo, de reuniones, de planes de acción, de enfoque de los proyectos..
Tanto si trabajamos con una consultora, como si contratamos a una persona, alguien interno de la empresa debe liderar (Lean Manager) el sistema junto a la dirección de la empresa.
En las primeras reuniones, el CEO de la empresa deberá implicar y liderar al equipo directivo.
Se deberá llevar a cabo un diagnóstico global del negocio de la empresa, elegir un proyecto piloto en alguna área o sección de la empresa para ver la “bondad” del sistema, y crear un departamento de mejora continua independiente a otras áreas del negocio y dependiente en la jerarquía de la empresa de la dirección.
FASES DE LA IMPLANTACIÓN:
En una primera fase (6 meses) podemos abordar proyectos piloto operativos basados en los distintos modelos que hemos visto:
- Lean Manufacturing: podemos elegir una actividad, sección o líneas de producción.
- Lean Office: podemos elegir un departamento favorable a este sistema como calidad.
- Lean Project: aquí podemos iniciarnos con I+D+IT o el departamento de ingeniería de proyectos.
En una segunda fase (18 meses) podemos extender el sistema LEAN al resto de la organización de forma paralela, de la siguiente forma:
- Extensión de los modelos operativos validados en los proyectos piloto, a todos los departamentos.
- Realización del proyecto Lean management mediante:
- Ejecución estratégica (definición, despliegue y seguimiento).
- Creación del sistema de gestión propio del negocio con indicadores.
- Implantación del proceso de gestión (diseño de la organización humana productiva (OHP), organigrama).
- Aumento de la productividad de la cadena de valor (reingeniería de procesos)
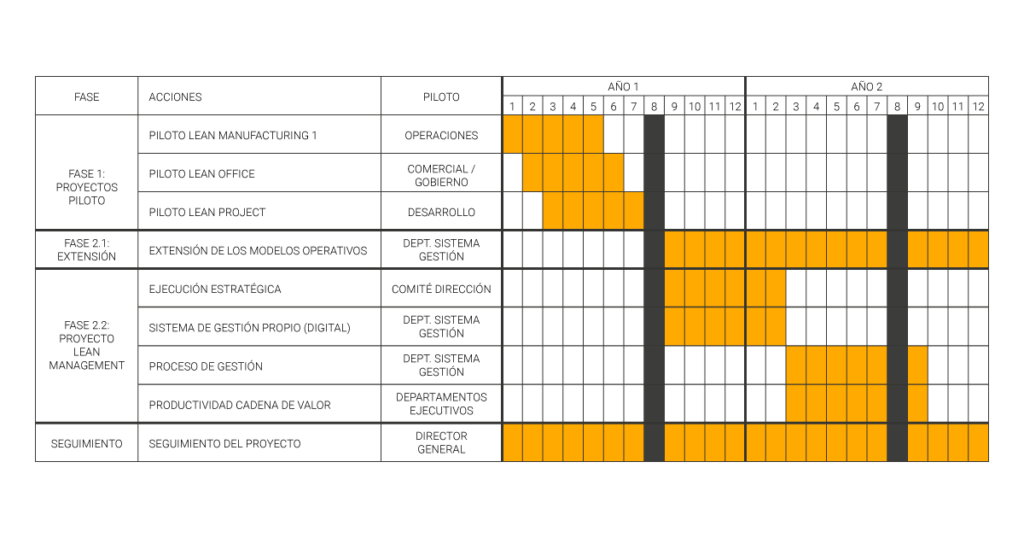
Normalmente se propone empezar por abajo (núcleos operativos) para que empiece a “calar” el sistema desde abajo, a que los responsables de producción por ejemplo y los operarios de línea sean capaces de asumir retos, a trabajar en equipo, a usar herramientas lean, a construir equipos kaizen.
Cuando esta fase inicial se pueda ir extendiendo a otras partes de la empresa, es cuando podremos aplicar el Lean Strategy con sus objetivos estratégicos hacia abajo.
EL PROYECTO PILOTO
El objetivo del proyecto piloto es implantar las bases de la mejora continua en un área acotada y controlable, y aumentar su productividad según los objetivos acordados, para descubrir los beneficios del Sistema LEAN, y abordar posteriormente el despliegue en toda la organización.
Las claves de este piloto son:
- Realizar un diagnóstico previo para escoger adecuadamente el área piloto.
- Definir claramente el GAP (Grupo Autónomo de Producción) y las personas implicadas:
- Integrantes del GAP (en ocasiones puede ser más de un GAP).
- El coordinador del GAP y el supervisor deben estar alineados con el proyecto para impulsar la consecución de los objetivos.
- El coordinador del GAP y el supervisor deben estar alineados con el proyecto para impulsar la consecución de los objetivos.
- El soporte debe ser claro y estar definido de antemano.
- Seleccionar los equipos de mejora, equipos kaizen (EK) a lanzar en el proyecto con su herramienta y sus objetivos definidos, que aseguren la rentabilidad del proyecto.
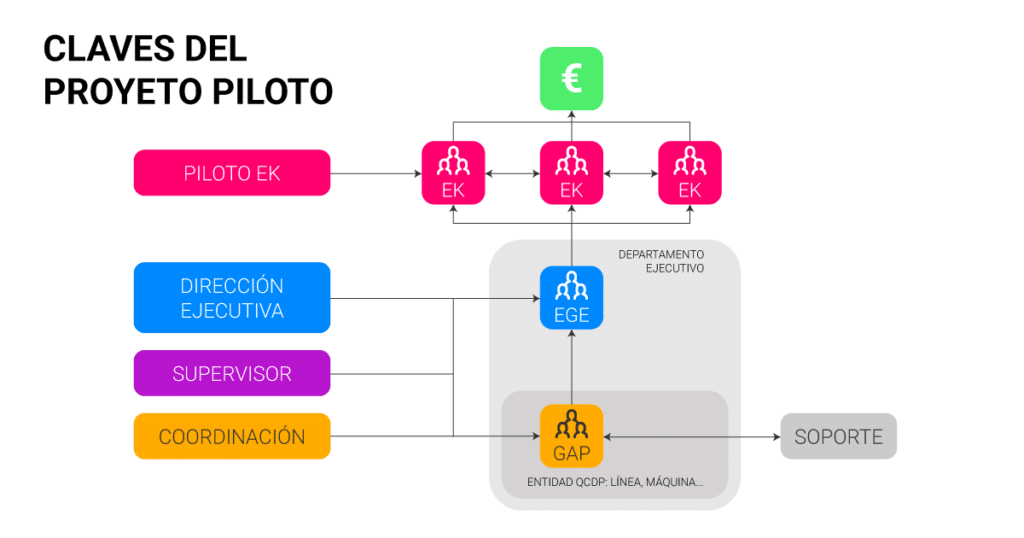
Cómo ejemplo tendremos: un equipo GAP (operativo) de una línea de envasado. En esta línea se trabajará en varios turnos (1,2 o 3) según la planificación, el volumen de trabajo, los pedidos, etc. Tendrá un coordinador (ej: responsable de línea) y por encima un supervisor (ej: jefe de envasado), y por encima de este el Director de producción de todas las áreas productivas de la empresa.
Como vemos en el ejemplo anterior, lo normal es empezar por un equipo productivo (Lean manufacturing), pero a pesar de que el piloto lo iniciemos con producción, los departamentos “soporte” (ej: mantenimiento y calidad) deben formar parte de este proyecto piloto y participar en el desarrollo del mismo.
Es habitual que la persona Lean Manager o Director de mejora continua salga de los departamentos de producción o de calidad.
No hay que olvidar que este sistema al final habrá que integrarlo con otros con los que cuente la empresa, como estándares de gestión de calidad (ISO9001), seguridad alimentaria (BRC, IFS)..
FASES DE IMPLANTACIÓN
Los pilotos suelen seguir este esquema.
- Fase 1: Formación.
Comunicar al equipo piloto en todos sus niveles el nuevo el sistema LEAN para gestionar el cambio, con acompañamiento sobre el terreno al supervisor y coordinador del GAP.
- Fase 2: Bases de la mejora continua
Despliegue de equipos operativos (GAPs) y control de los objetivos mediante la definición de los indicadores clave (KPIs) y las reuniones Top 60/15 en el departamento.
Despliegue de las herramientas de GAP (5S, ideas de mejora, polivalencia y tablero de marcha).
- Fase 3: Mejora de los resultados
Enfoque a los resultados mediante equipos kaizen y herramientas de productividad desplegados en el GAP piloto del departamento seleccionado. Talleres lean.
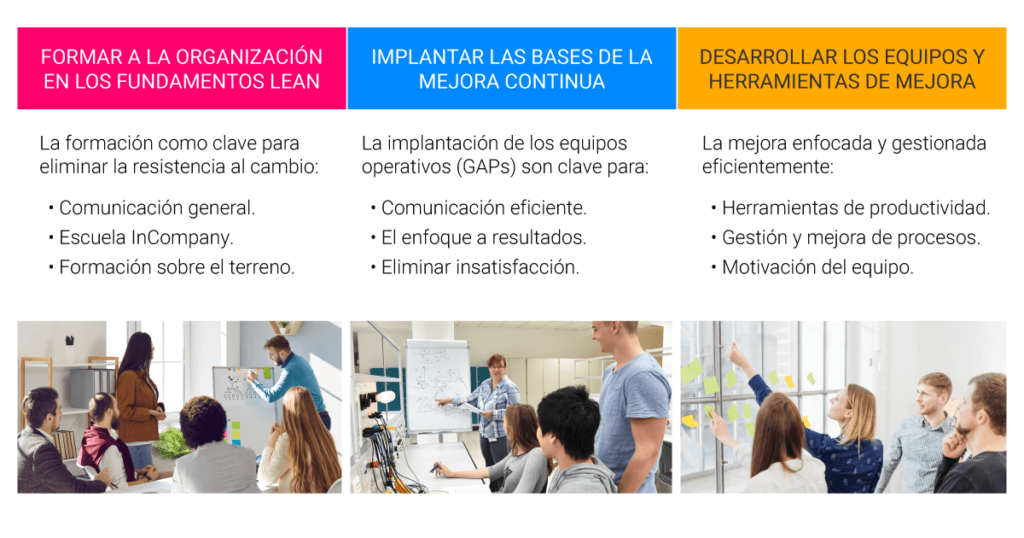
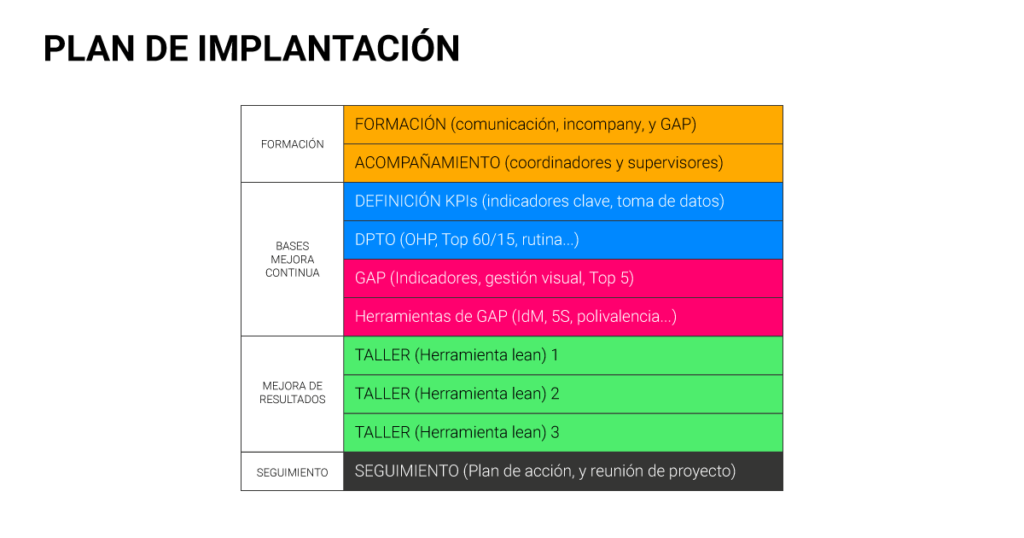
Como hemos visto lo primero es la formación, luego se implementan bases de mejora continua donde se determina cuáles son los indicadores, la organización, las rutas de comunicación, se establecen la gestión visual, los tableros con los indicadores (KPIs), si son digitalizados mucho mejor, y luego las propias herramientas de los equipos (5 S, matriz de polivalencias, etc.).
Luego por último finalizaremos el proyecto piloto aplicando herramientas específicas en producción, en office…
Los aspectos claves para que sea un éxito este piloto y la dirección de la empresa quiera extenderlo a la organización es que:
- Hagamos una buena gestión del mismo, estableciendo:
- Plan de acción: destinado a la formalización de acuerdos en caso de desviación del plan.
- Agenda semanal: consensuada con los implicados, y enviada con 1 semana de antelación por correo.
- Demostrar la bondad:
- Cambio cultural: nueva forma de trabajar, nuevas actitudes, nuevos roles/hábitos/rutinas.
- Impacto en productividad/ahorros: mediante el uso de indicadores de productividad enfocado a ahorros económicos:
COMPROMISO CON LOS RESULTADOS:
Cálculo de ahorros económicos (€):
El impacto económico de las acciones derivadas de la aplicación de la mejora continua debe ser calculado de la forma siguiente:
- Definir un indicador de productividad (OEE, pph, mermas…)
- Fijar un punto de partida o referencia.
- Monitorizar la evolución semanal del indicador.
- Calcular la evolución real frente a la referencia.
- Extrapolar anualmente el resultado de la última 4 semanas.
Este blog es continuación del blog:
- Metodología Lean en Sector alimentario. Introducción a la metodología
- Lean II: Espíritu Kaizen
- Lean III: Mecanismos del sistema Lean
IRISTRACE es un software que te va a permitir aplicar la mejora continua en los procesos y llevar los controles en planta y justificar dichos registros totalmente de forma digital, sin el uso de papeles, ni retrabajos que no aportan valor al departamento de calidad y supone un tiempo perdido que se puede dedicar a otras tareas del departamento.